3D printing in the healthcare sector: an enabling technology
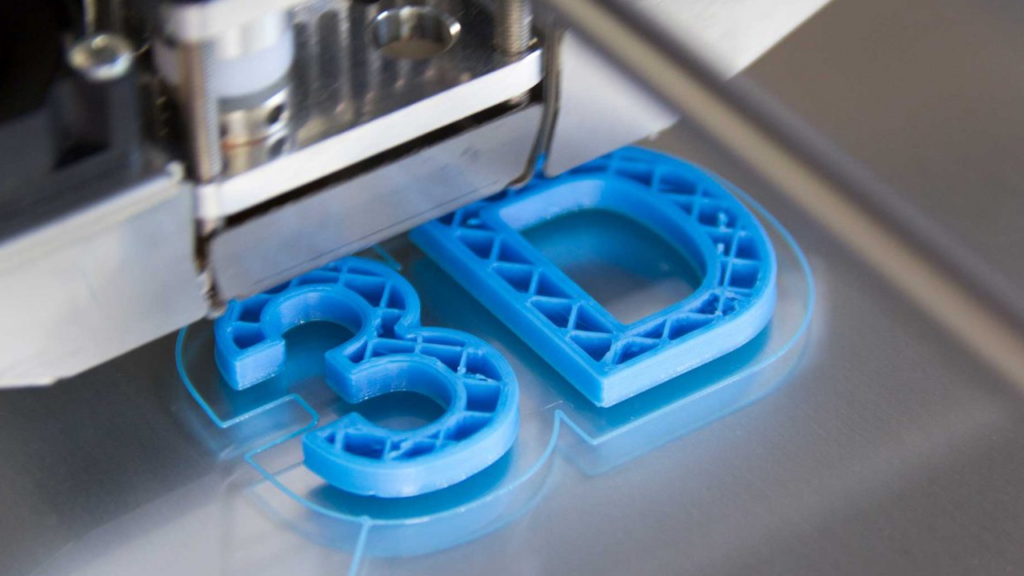
3D printing is one of the technologies most present in the health area. The company Formlabs, estimates that more than 90% of the main medical device companies use 3D printing for the elaboration of their devices, being more precise and creating better prototypes, This comes to complement the existing biological structures.
One of the most important uses of 3D printing in the medical industry is for the manufacture of orthopedic implants. Whether for arms, legs, hips, 3D printing allows customized parts of the same for the patient to obtain better results and higher quality in their treatment. The molds printed with this technology, in most cases, are the most hygienic and accessible option. Some companies that contribute with the printing process today are Stratasy, GE Additive, 3D Systems, Materialise y EOS. In turn, 3D Printing, collaborated with the need for sanitary materials during COVID-19. Thanks to it, individual protection supplements have been manufactured, such as face and eye protection visors, masks, among other sanitary solutions. Respiratory valves have also been created after their exhaustion due to the collapse of hospitals and patients seriously affected by the virus.
As for the surgical field, surgeries must be prepared and adapted to each patient, which is why customized tools cost a lot of time and money. Without customized parts, the doctor’s responsiveness and availability to the patient is diminished. Thanks to 3D printing, these customized surgical tools can be prepared up to date and tailored to the patient’s body. A successful case of this was at the Bicetre Hospital: Dr. Marc Soubeyrand created his own auxiliary tools in nylon with a 3D printer in order to provide the implants with the best position during surgery. Using a CT scan, he converts the images into a 3D file, to adapt the measurements and create the tools for the operation.
Although there are impediments associated with regulatory approvals for the use of these materials, companies continue to rely on this method to customize consultations, customize parts for patients, and improve production costs.